Imagine a bustling construction site. Towering cranes hoist materials, skilled workers navigate the intricate web of scaffolding, and progress takes shape before your very eyes. But what you might not realize is the unsung hero behind this symphony of activity: the scaffolding plank roll forming machine.
Function of Scaffolding Plank Roll Forming Machine
In essence, a scaffolding plank roll forming machine is a metalworking marvel that continuously produces the very foundation upon which construction workers stand – the scaffolding planks. These machines take pre-cut steel coils and, through a series of automated processes, transform them into the sturdy, dependable platforms that ensure worker safety and project efficiency.
Here’s a breakdown of the key functions of a scaffolding plank roll forming machine:
- Le dévoilement : The machine begins by unwinding the steel coil from a designated holder.
- Mise à niveau : Any unevenness in the sheet metal is meticulously ironed out to ensure a smooth and consistent material flow.
- Servo Feeding: High-precision servo motors precisely guide the leveled steel into the forming process.
- Poinçonnage : Strategically placed punches create holes or indentations in the steel, adding strength and functionality to the final plank.
- Continuous Roll Forming: The heart of the machine, a series of forming rollers progressively bend and shape the steel into the desired profile of a scaffolding plank.
- Automatic Cutting: Once the desired length is reached, the machine automatically severs the formed plank, ready for stacking or further processing.

Types of Scaffolding Plank Roll Forming Machines
The world of scaffolding plank roll forming machines isn’t a one-size-fits-all scenario. Manufacturers offer a variety of options to cater to specific production needs and budget constraints. Here’s a glimpse into the two main types:
- Hydraulic Punching Machines: These machines utilize hydraulic pressure to activate the punching mechanism. They offer slower production speeds (around 4 meters per minute) but are generally more affordable.
- Mechanical Punching Machines: These machines rely on a mechanical drive system for punching, resulting in faster production speeds (up to 10 meters per minute). However, they tend to come with a higher price tag.
Applications of Scaffolding Plank Roll Forming Machines
The impact of scaffolding plank roll forming machines extends far beyond construction sites. Here are some of the many applications where these machines play a crucial role:
- Industrie de la construction : This is undoubtedly the primary domain for scaffolding planks. They provide safe and sturdy platforms for workers to navigate various heights while constructing buildings, bridges, and other structures.
- Shipbuilding and Repair: Scaffolding planks find use in shipyards, offering temporary walkways and platforms for workers to access different sections of vessels under construction or repair.
- Event Production: Concerts, festivals, and other large-scale events often require temporary structures. Scaffolding planks, thanks to their versatility and ease of assembly, are instrumental in creating these temporary platforms and stages.
- Oil and Gas Industry: Refineries and offshore platforms utilize scaffolding planks for maintenance and inspection purposes, ensuring worker safety at these critical infrastructures.
Avantages de la Scaffolding Plank Roll Forming Machines
Compared to traditional methods of plank production, scaffolding plank roll forming machines offer a multitude of advantages:
- Efficacité accrue : These machines automate the entire plank-forming process, significantly boosting production rates compared to manual labor.
- Qualité constante : The automated nature of the machines guarantees consistent plank dimensions and quality, ensuring structural integrity and worker safety.
- Réduction des coûts de main-d'œuvre : By automating production, the need for a large workforce is minimized, leading to significant cost savings.
- Material Optimization: Roll forming machines minimize material waste, maximizing the utilization of steel coils and reducing overall production costs.
- Increased Safety: Standardized plank sizes and consistent quality contribute to a safer working environment for construction personnel.
-
Machine de formage de rouleaux de tubes à souder
-
Machine de profilage de panneau de porte de garage
-
Ligne de coupe à longueur
-
Canal en U en acier inoxydable pour machine de support de fenêtre en verre
-
Machines de formage de la série de boîtes de volets
-
Machine de formage de rouleaux de tube d'auvent
-
Profileuse de cadre de porte en métal Double feuillure
-
Machine de formage de rouleaux de tuyaux octogonaux de porte d'obturation
-
Rouleau de rail de guidage en acier galvanisé formant la machine
Considerations When Choosing a Scaffolding Plank Roll Forming Machine
Investing in a scaffolding plank roll forming machine is a significant decision. Here are some key factors to consider:
- Capacité de production : Evaluate your anticipated plank production needs and choose a machine that can meet those demands efficiently.
- Plank Specifications: Ensure the machine can produce planks that adhere to the specific size and strength requirements of your target market.
- Caractéristiques de la machine : Consider factors like punching capabilities, forming speed, and ease of operation when making your selection.
- Budget : Scaffolding plank roll forming machines range in price depending on features and capabilities. Determine your budget and choose a machine that offers the best value for your investment.
- Support après-vente : Reliable after-sales support is crucial for ensuring the smooth operation and longevity of your machine. Research the manufacturer’s reputation and service network before making a purchase.
Suppliers of Scaffolding Plank Roll Forming Machines and Pricing Considerations
Finding the right supplier for your scaffolding plank roll forming machine is just as important as selecting the machine itself. Here’s a breakdown of some key considerations:
- Réputation et expérience : Look for established manufacturers with a proven track record in the industry. Their experience translates to reliable machine design, functionality, and after-sales support.
- Personnalisation de la machine : Some manufacturers offer the ability to customize machines to meet specific production needs. This might involve tailoring the roll forming profile for unique plank designs or integrating additional punching functionalities.
- Global Reach vs. Local Suppliers: While globally recognized manufacturers offer wider warranties and potentially advanced features, local suppliers might provide faster delivery times and potentially lower costs due to reduced transportation expenses. Consider the trade-off between features and accessibility when making your choice.
Sample Pricing of Scaffolding Plank Roll Forming Machines (Estimated):
Disclaimer: It’s important to note that pricing for scaffolding plank roll forming machines can vary depending on factors like features, customization options, negotiation terms, and even fluctuations in material costs. The following figures are meant to provide a general guideline:
- Basic Hydraulic Punching Machine: Starting around $30,000 USD
- Hydraulic Punching Machine with Advanced Features: $50,000 USD and above
- Basic Mechanical Punching Machine: $40,000 USD and above
- High-Speed Mechanical Punching Machine: $70,000 USD and above
Rappelez-vous : These are just ballpark figures. For the most accurate pricing information, it’s always best to contact reputable scaffolding plank roll forming machine manufacturers directly and request quotes based on your specific requirements.
Advantages and Disadvantages of Different Scaffolding Plank Roll Forming Machine Types
Hydraulic Punching Machines:
Avantages :
- Lower Cost: Generally more affordable compared to mechanical punching machines.
- Simpler Design: Hydraulic systems can be less complex, potentially leading to easier maintenance.
Inconvénients :
- Slower Production Speed: Limited by the hydraulic actuation process, resulting in slower plank formation rates.
- Potentially Higher Energy Consumption: Hydraulic systems might require more energy to operate compared to mechanical counterparts.
Mechanical Punching Machines:
Avantages :
- Faster Production Speed: Mechanical drive systems enable faster roll forming and higher production outputs.
- Potentially Lower Energy Consumption: May require less energy to operate compared to hydraulic systems.
Inconvénients :
- Higher Cost: The mechanical design and components can lead to a higher initial investment.
- Potentially More Complex Maintenance: Mechanical systems might require more specialized maintenance expertise.
The Right Choice for You:
The ideal machine type depends on your specific needs. If affordability is a primary concern, a hydraulic punching machine might be a suitable choice. However, if production speed is paramount, a mechanical punching machine would be a better fit. Consider your budget, production volume, and long-term maintenance requirements when making this decision.
Beyond the Basics: Advanced Features of Scaffolding Plank Roll Forming Machines
While the core functionality of scaffolding plank roll forming machines revolves around uncoiling, leveling, forming, and cutting steel, some advanced features can enhance your production capabilities and product quality:
- Automatic Stacking System: This feature automatically stacks the formed planks, saving labor and streamlining the production process.
- Computerized Control System: A user-friendly computer interface allows for precise control over machine parameters, monitoring of production data, and easier operation.
- Pre-Punching Capability: Some machines offer the ability to punch holes or slots before the forming process, allowing for additional customization of the final plank profiles.
- Run-Out Table: An extended table facilitates the smooth movement and stacking of formed planks, especially with high-speed machines.
Autres considérations :
The availability and cost of these advanced features can vary depending on the manufacturer and machine model. Carefully evaluate your needs and weigh the return on investment before opting for these functionalities.
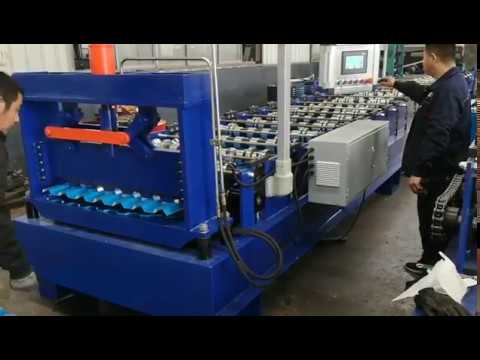
FAQ
Q: What safety standards should scaffolding planks comply with?
A : Scaffolding planks must adhere to specific safety standards established by regulatory bodies in your region. Common standards include EN 1004 (Europe), ASTM F925 (North America), and AS/NZS 1576 (Australia/New Zealand). Ensure your chosen machine produces planks that meet the necessary safety certifications for your target market.
Q: What are the ongoing maintenance requirements for a scaffolding plank roll forming machine?
A : Regular maintenance is crucial for ensuring the smooth operation and longevity of your machine. The specific maintenance schedule will vary depending on the machine model and usage patterns.
Q: What are the typical lead times for receiving a scaffolding plank roll forming machine after placing an order?
A : Lead times can vary depending on the complexity of the machine, customization options, and current production capacity of the manufacturer. Generally, lead times range from 4 to 12 weeks for standard machines. More complex or custom-built machines might require longer lead times.
Q: Does using a scaffolding plank roll forming machine require specialized skills to operate?
A : While some basic mechanical knowledge is beneficial, most modern scaffolding plank roll forming machines are designed for user-friendly operation. Manufacturers typically provide comprehensive training manuals and on-site operator training to ensure proper machine operation and maintenance.