Imagine a machine that can transform a flat sheet of metal into a precisely shaped octagonal tube, the backbone of countless roller shutter doors. That’s the magic of the octagonal tube forming machine, a marvel of metal manipulation that might seem complex at first glance, but holds the key to security and convenience in everyday life.
This article dives deep into the world of octagonal tube forming machines, exploring their function, different types, applications, and the nitty-gritty details like suppliers and pricing. We’ll answer all your burning questions and equip you with the knowledge to navigate this niche yet crucial piece of industrial machinery.

Function of Octagonal Tube Forming Machines
At its core, an octagonal tube forming machine is a metalworking marvel. It takes a coil of sheet metal, typically steel or aluminum, and progressively bends and shapes it into an eight-sided tube. This is achieved through a series of forming stations, each equipped with specially designed rollers that gradually transform the flat sheet into the desired octagonal profile.
Think of it like origami on an industrial scale. The machine folds and shapes the metal with incredible precision, ensuring the final product is not only structurally sound but also boasts consistent dimensions throughout its length.
Here’s a breakdown of the typical octagonal tube forming machine process:
- Uncoiling: The metal coil is fed into the machine, unwinding from its initial form.
- Straightening: Any slight bends or imperfections in the sheet metal are ironed out to ensure a smooth starting point.
- Forming Stations: The metal is progressively fed through a series of rollers that bend and shape it into the octagonal profile. Each station builds upon the previous one, achieving the final form gradually.
- Welding (Optional): Depending on the desired strength and application, the seam of the octagonal tube might be welded shut for a seamless finish.
- Cutting: The formed tube is cut to the desired length using an integrated cutting mechanism.
- Stacking or Coiling: The finished octagonal tubes are either stacked for easy retrieval or coiled for further processing or storage.
The entire process is automated and controlled by a computer program, ensuring consistent quality and high production rates.
the Different Types of Octagonal Tube Forming Machines
Not all octagonal tube forming machines are created equal. They come in various configurations to cater to different production capacities, material types, and desired tube dimensions. Here’s a breakdown of the two main types:
- Fixed-Size Machines: These workhorses are designed to produce octagonal tubes of a specific size. They offer exceptional production speed and efficiency when dealing with large quantities of tubes with the same dimensions. Imagine a factory churning out octagonal tubes for a standardized line of roller shutters – a fixed-size machine would be the perfect fit.
- Adjustable-Size Machines: As the name suggests, these versatile machines can be configured to produce octagonal tubes of various sizes. This flexibility comes at the cost of slightly slower production speeds compared to fixed-size machines. However, for manufacturers dealing with diverse projects requiring different tube dimensions, adjustable-size machines offer unmatched adaptability.
Additional Considerations:
Beyond fixed versus adjustable, there are other factors to consider when choosing an octagonal tube forming machine:
- Material Compatibility: Ensure the machine can handle the type of metal you plan to use, such as steel, aluminum, or even specific alloys.
- Wall Thickness: Different machines cater to varying wall thicknesses for the octagonal tubes. Consider the structural requirements of your application.
- Production Speed: How many tubes do you need to produce per hour? Match your machine’s capabilities to your production goals.
- Automation Level: Some machines offer features like automatic loading and unloading, reducing manual labor and increasing efficiency.
The Applications of Octagonal Tube Forming Machines
While roller shutters are the most common application of octagonal tubes, their uses extend far beyond securing your storefront. Here are some other areas where you might encounter these versatile tubes:
- Construction: Octagonal tubes are used for lightweight yet sturdy support structures, fencing applications, and even handrails.
- Furniture: The unique shape and strength of octagonal tubes can be incorporated into furniture designs, adding a touch of industrial chic.
- Automotive: Certain vehicle components, particularly in off-road applications, can benefit from the lightweight strength of octagonal tubes.
- Signage and Displays: The clean lines of octagonal tubes make them suitable for constructing display stands and signage frameworks.
The possibilities are truly endless, limited only by the imagination of designers and engineers.
-
Garage door panel roll forming machine
-
Double deck roll forming machine
-
Green modern Agriculture gutter panel roll forming machine with tank chain
-
Omega roof batten Top hat channel roll forming machine
-
Roll forming machine China for Automatically PPGI Fence Panel
-
Roll forming machine company for Fence guide Rail
-
Roll forming machine cost for Fence post guide rail good price
-
Stainless U Channel for Glass Window Supporter Machine
-
High speed PPGI corrugated sheet roll forming machine
Suppliers and Pricing of Octagonal Tube Forming Machine
Now that you understand the different types and capabilities of octagonal tube forming machines, it’s time to delve into the practicalities. Here, we’ll explore some of the key players in the market and shed light on the pricing considerations when acquiring this valuable machinery.
Major Suppliers of Octagonal Tube Forming Machines:
The global market for octagonal tube forming machines is dominated by a handful of established manufacturers, primarily concentrated in China. Here are some of the leading names:
- Jiangsu Huazhong Roll Forming Machine Co., Ltd.: A prominent Chinese manufacturer offering a range of octagonal tube forming machines, known for their focus on customization and affordability.
- LOTOS Forming Machinery Manufacturing: Another major Chinese player, LOTOS prides itself on high-quality machines and efficient after-sales service.
- Dallan Spa: An Italian manufacturer known for its innovative approach and focus on advanced automation features in their tube forming machines. While not solely focused on octagonal tubes, Dallan offers machines with the capability to produce them.
Finding the Right Supplier:
Choosing the right supplier for your octagonal tube forming machine doesn’t solely depend on brand recognition. Here are some key factors to consider:
- Machine Specifications: Ensure the machine aligns with your production needs in terms of size adjustability, material compatibility, and desired output speed.
- Reputation and Experience: Research the supplier’s track record and customer reviews to gauge their reliability and expertise in octagonal tube forming technology.
- After-Sales Support: A reliable supplier will offer comprehensive after-sales support, including spare parts availability and technical assistance, to keep your machine running smoothly.
- Pricing and Payment Terms: Compare prices from various suppliers and consider factors like financing options and potential import duties (if applicable).
Octagonal Tube Forming Machine Pricing:
The cost of an octagonal tube forming machine can vary significantly depending on several factors, including:
- Machine Type: Fixed-size machines are generally more affordable than adjustable-size machines due to their simpler design.
- Production Capacity: Machines with higher output speeds tend to come with a heftier price tag.
- Level of Automation: Machines with features like automatic loading and unloading systems naturally cost more than their manual counterparts.
- Brand and Location: Machines from established European manufacturers might carry a premium compared to those from Chinese suppliers.
As a general estimate, expect to pay anywhere between USD $20,000 and USD $100,000 for a basic octagonal tube forming machine. For highly automated and versatile machines capable of handling a wide range of sizes and materials, the price can climb to USD $150,000 or even higher.
Additional Costs to Consider:
Beyond the initial machine purchase, factor in additional costs such as:
- Shipping and Installation: Depending on the supplier location and machine size, shipping and installation can add a significant sum to the overall cost.
- Tooling: Different size tubes might require specific tooling for the forming stations, adding to the initial investment.
- Maintenance: Regular maintenance is crucial for optimal performance. Factor in the cost of spare parts and potential service contracts.
The Takeaway:
Purchasing an octagonal tube forming machine is a significant investment. By carefully considering your production needs, researching suppliers, and understanding the associated costs, you can make an informed decision that empowers your business and unlocks the potential of these versatile machines.
Advantages and Limitations of Octagonal Tube Forming Machines
Every industrial machine has its own set of pros and cons. Let’s explore the advantages and limitations of octagonal tube forming machines to help you decide if they’re the right fit for your needs.
Advantages:
- Efficiency and Speed: Compared to traditional fabrication methods, octagonal tube forming machines offer a faster and more automated way to produce consistent, high-quality tubes.
- Reduced Labor Costs: Automation translates to less reliance on manual labor, potentially reducing overall production costs.
- Material Versatility: Many machines can handle various materials like steel, aluminum, and even some alloys, offering production flexibility.
- Consistent Quality: The controlled forming process ensures consistent dimensions and structural integrity throughout the length of the octagonal tube.
- Reduced Waste: Compared to manual cutting and fabrication methods, octagonal tube forming machines minimize material waste.
Limitations:
- Initial Investment: As discussed earlier, purchasing an octagonal tube forming machine requires a significant upfront investment.
- Floor Space Requirements: These machines can have a substantial footprint, so ensure you have adequate space for installation and operation.
- Skillset for Operation: While the machines are automated, some level of training is necessary for operators to ensure proper setup, maintenance, and troubleshooting.
- Complexity of Adjustments: For adjustable-size machines, changing tube dimensions might involve adjustments to various forming stations, requiring some technical know-how.
- Maintenance Needs: Regular maintenance is essential for optimal performance and longevity of the machine. Factor in the cost of spare parts and potential service contracts.
- Limited Resale Market: Octagonal tube forming machines are specialized pieces of equipment, and the resale market might be limited compared to more general-purpose machinery.
Making the Right Choice:
The decision to invest in an octagonal tube forming machine hinges on your specific production needs and budget. If you require high volumes of consistent, high-quality octagonal tubes, and have the space and resources to accommodate the machine, the advantages of efficiency, reduced labor costs, and consistent quality might outweigh the limitations.
However, for smaller production runs or if your needs are less specialized, exploring alternative fabrication methods or outsourcing tube production might be a more cost-effective solution.
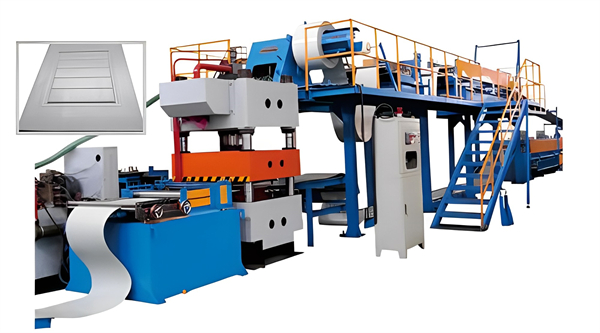
FAQ
Q: What are the typical applications of octagonal tubes formed by these machines?
A: As explored earlier, octagonal tubes have a surprisingly wide range of applications. Here’s a quick recap:
- Roller shutters: The most common application, octagonal tubes form the backbone of these security and weatherproofing barriers for doors and windows.
- Construction: They can be used for lightweight support structures, fencing, and even handrails due to their favorable strength-to-weight ratio.
- Furniture: The unique shape and strength of octagonal tubes can be incorporated into furniture designs, adding an industrial or modern aesthetic.
- Automotive: Certain vehicle components, particularly in off-road applications, benefit from the lightweight strength of octagonal tubes.
- Signage and Displays: The clean lines of octagonal tubes make them suitable for constructing display stands and signage frameworks.
Q: Are there any safety precautions to consider when operating an octagonal tube forming machine?
A: Absolutely. As with any industrial machinery, safety is paramount. Here are some key safety considerations:
- Proper training: Operators should receive thorough training on the safe operation and maintenance of the machine.
- Personal protective equipment (PPE): Operators should wear appropriate PPE such as safety glasses, gloves, and hearing protection when operating the machine.
- Machine guarding: Ensure all safety guards and enclosures are in place and functioning properly before operating the machine.
- Emergency stop procedures: Operators should be familiar with the emergency stop procedures in case of malfunctions or accidents.
Q: How long do octagonal tube forming machines typically last?
A: The lifespan of an octagonal tube forming machine depends on various factors, including the quality of the machine, maintenance practices, and overall usage. With proper care and maintenance, a well-built machine can last for decades.
Q: What are some of the emerging trends in octagonal tube forming technology?
A: The industry is constantly evolving, and here are some exciting trends to watch:
- Increased automation: We can expect to see even more automation features integrated into octagonal tube forming machines, further reducing manual labor and improving production efficiency.
- Advanced material compatibility: Machines with the capability to handle a wider range of materials, including high-strength steels and lightweight alloys, are on the horizon.
- Integration with Industry 4.0: The future might see octagonal tube forming machines seamlessly integrated into Industry 4.0 workflows, enabling real-time monitoring, data analysis, and predictive maintenance.
By staying informed about these trends, you can ensure your octagonal tube forming operations remain at the forefront of efficiency and technological advancement.
Conclusion
Octagonal tube forming machines are more than just industrial workhorses. They represent a technological marvel that transforms flat sheets of metal into the building blocks for countless applications. From securing our storefronts to lightweight yet sturdy structures, octagonal tubes play a vital role in our modern world.
Understanding the function, types, and considerations surrounding these machines empowers manufacturers to make informed decisions and unlock the potential for efficient, high-quality octagonal tube production. As technology continues to evolve, the future of octagonal tube forming machines promises even greater automation, versatility, and integration with the ever-evolving industrial landscape.